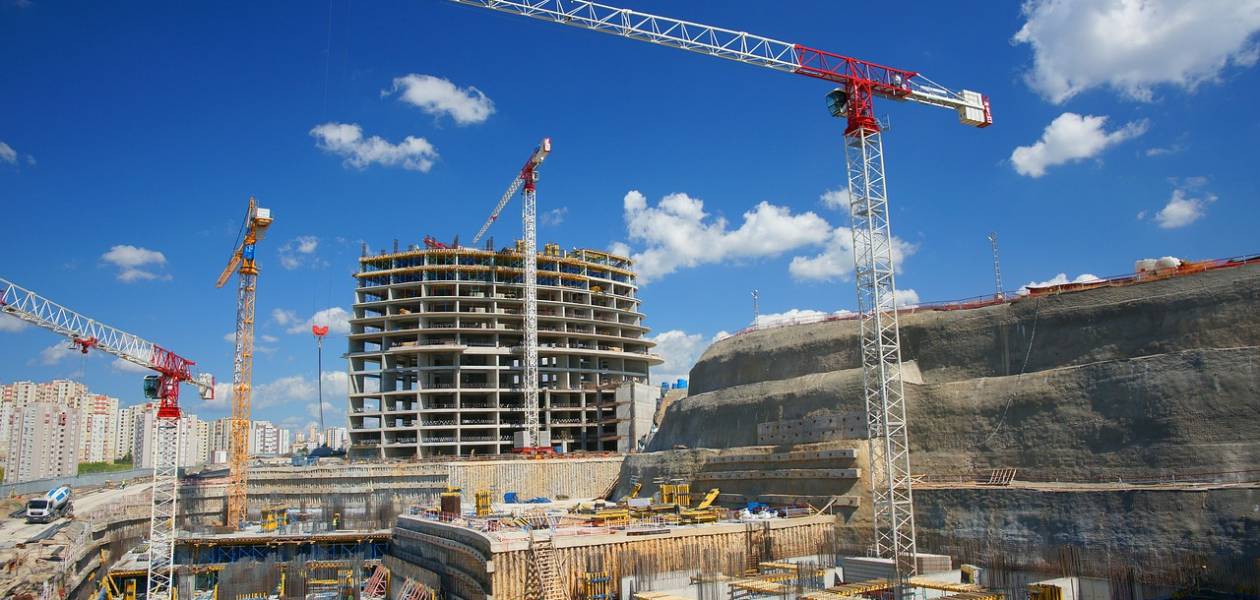
- The growing global population and urbanization will require more construction in the coming years and decades. And as a consequence, more cement.
- Currently, the concrete and cement industry accounts for approximately 7% of global CO2 emissions, and if no action is taken, this number could grow dramatically.
- US-based start-up Sublime Systems is 'electrifying cement production and forgoing the kiln entirely' — which is the most energy and fossil fuel-intensive part of the cement manufacturing process.
"Population growth and urbanization are driving the construction of cities equivalent to the size of New York City every month," Nollaig Forrest, the Chief Sustainability Officer at Holcim, noted in a recent report.
"Cement is a key ingredient in concrete, which is the most used construction material because it is local, affordable, versatile, recyclable, high-performing and resilient," she adds.
"But getting the materials to produce cement and concrete is putting increased pressure on our planet and its natural resources."
Concrete and cement account for approximately 7% of global CO2 emissions, and if no action is taken, this number could grow dramatically, effectively undercutting decarbonization efforts in other sectors.
The World Economic Forum, in collaboration with Boston Consulting Group and industry input from the Global Cement and Concrete Association (GCCA), has examined the manufacturing and use of concrete to develop a seven-part framework that helps scale low-carbon design and reduce emissions from cement and concrete production.
It suggests pulling three key levers to reduce concrete emissions in construction projects by up to 40% by 2030:
1. Manufacturing process decarbonization, including tactics such as production efficiency and renewable electricity.
2. Specifying lower-carbon cement blends, which use supplementary cementitious materials to reduce the volume of cement in production, thus reducing the blend's carbon footprint.
3. Optimizing the volume of material used in projects by applying design techniques that reduce the overall volumes of material required and balancing trade-offs between the carbon intensity of cement products and the required volumes.
Dr Leah Ellis represents one such solution towards decarbonising the manufacturing process by changing how cement is produced. As co-founder and CEO at US-based startup Sublime Systems, Leah says they are building the 'electric vehicle of cement-making'.
"We replace the fossil fuel kiln with an electric chemical approach," she tells the Forum.
The most common method to produce cement today creates two sources of CO₂ emissions: about 40% comes from the burning of fossil fuels to heat kilns at 1300-1450°C, and about 60% is released during the thermal decomposition of limestone into carbon dioxide and lime, an essential element of clinker which is the main ingredient of cement (about 70%).
"We're replacing a high-temperature, combustion-fuelled, fossil-fuelled kiln with an ambient temperature process that can be more efficient thermodynamically and make the same hardened cement that we've been using for millennia," Leah says.
"And we can ultimately make it at the same cost."
From 100 tonnes a year to 100 tonnes daily
This approach to cement-making has been proven in the lab, and the team now remains focused on building scale. "We have scaled up in the past three years from a gram of cement in the lab to 100 tons per year in our pilot plant. But that is still a drop in the bucket," Leah admits.
"We have to go from our pilot plant capacity today to a demonstration-scale capacity - so this is the minimum viable industrial scale plant, which is about 100 tonnes daily.
"And from there, we have to scale up to a million tonnes per year if we need to be relevant in the industry, produce relevant volumes and compete on cost."
But she remains optimistic about the industry moving from chemistry-based standards to performance-based standards. "That means you're defining cement not just by its chemistry but by its properties," she says.
"So, does this cement react with water in the same ratios? Does it harden and form a gel in the same amount of time? Does it have the same strength and durability measured by specific tests?
Why is this important? "Because defining cement by its performance and not its chemistry allows you to solve the real problem: to have a high-performance, low-carbon building material."
Towards 'true' zero carbon
For Leah, developing the technology behind sustainable cement production came from a passion for chemistry and the desire to minimise her environmental impact.
"I wasn't a cement expert when I started Sublime Systems," she says. "I was a battery expert and had to learn about cement from Wikipedia, textbooks and then journal articles and by getting deeper and deeper into it."
Today, their cement aims to achieve 'true' zero carbon — rather than just 'net' zero — by replacing the fossil fuels kiln with an electrochemical process and by avoiding CO₂ emissions in the first place. "We're creating a technology for a post-carbon world.
"This technology is not just for between now and 2050 when we get to net zero. It's a technology that will be relevant 100 years and even a millennia from now."
And Leah believes her journey carries a lesson for everyone: "Good ideas can come from anywhere. I would encourage people to colour outside the lines and to try to solve problems, even if they may not be an expert."
Check out our Net-Zero Industry Tracker to monitor the top priorities for the cement industry and track progress in other sectors.
Author :
Pooja Chhabria - Digital Editor, World Economic Forum
Posted on 2023-11-10 16:18
Comments